Discover the hidden with X-ray inspection
Non-destructive cross-sections thanks to 3D CT X-ray inspection
The ARIRANG series generates a 3D CT X-ray image in just 15 seconds, making it one of the fastest industrial CT systems currently available. In addition to their speed, the systems impress with outstanding detail recognition and maximum precision. This means that they not only meet the requirements of SMD inspection, but also the challenges of semiconductor inspection. Digital cross-sections can be created using 3D reconstruction and defects can be measured precisely in all three dimensions.
That's why you need X-ray inspection
Discover hidden errors
Optical inspection systems (AOI and SPI) are now standard in electronics production, but when it comes to inspecting processors such as BGAs, LGAs and ICs, these systems reach a limit: soldering defects cannot be assessed with optical inspection systems for components whose connections are under the housing body, as they can only inspect the component externally - even with side cameras.
Only X-ray inspection makes it possible to see what is underneath a component. And X-ray inspection in the SMD industry is becoming increasingly relevant due to the advancing digitalization of our living environment: Everyday objects such as the handbrake, for example, which until a few years ago were operated mechanically, are now controlled electrically - with printed circuit boards on which processors with concealed solder joints are installed. X-ray inspection is needed to detect defects caused by faulty solder joints in these components, some of which are critical to safety.
Interesting facts about X-ray inspection
How much power does X-ray inspection really need in SMD production and what is the difference between online, inline and offline inspection? And how does image creation work with 2D, 2.5D and 3D CT X-ray?
We'll tell you!
Offline, Online and Inline – Three types of industrial x-ray inspection
Industrial X-ray systems for electronics manufacturing can be grouped into three types: Offline systems (manual systems), Online systems and Inline systems. It depends on the individual inspection requirements which system is the best fit.
Offline Xray
Offline X-ray systems, also called manual X-ray systems (MXI), are especially suitable for spot checking assemblies. With manual X-ray inspection, each step of the inspection proces is executed by the operator – from placing the test object into the system to targeting the region-of-interest (ROI) to the evaluation of the inspected assembly. Manual X-ray inspection systems are the most affordable X-ray systems and are thus well suited as an entry into X-ray inspection.
Online X-ray
Online systems are X-ray systems, that, while not being integrated into the production line and having to be manually loaded and unloaded, can already run automated inspection routines (automated X-ray inspection, AXI). Online systems target the ROI automatically, adjust angle and contrast and create an X-ray image. The evaluation, wheter the inspected part is good or not good, is done by the operator. Online X-ray systems are suitable for productions with high quantities, e.g. for inspecting every umpteenth PCB of a job. Thus, online systems can also be used for process control, since conclusions can be drawn about the process from the inspection results.
Inline X-ray
Inline X-ray systems are fully automated X-ray systems, that are integrated into the production line. The printed circuit boards to be tested are fed into the system fully automatically, inspected and evaluated with the aid of test routines, and likewise automatically transported out of the system. The inspection results are saved in a data base. With inline X-ray systems100% control of product quality (inspection of every printed circuit board produced) can be realized. 100% product quality control is especially recommended for components used in safety-critical industries such as medical technology or the automotive sector.
Structure and mode of operation
Every industrial x-ray system consists of an X-ray source (or X-ray tube), a detector for image generation and a table or conveyor belt for the test object.
Depending on the system, the x-ray tube is placed either at the top or bottom of the system, the detector is always placed on the opposite site of the X-ray tube. The test object is always located in between the X-ray tube and the detector.
To produce an X-ray image, the X-ray source emits X-rays at a specific angle. These X-rays pass through the test object and hit the detector, who converts the incoming X-rays into gray scale values. Depending on the components that the X-rays have passed through, the radiation is weakened. The denser the component, the weaker the X-rays hitting the detector. The detector converts weak X-rays (dense areas) to darker grays values, stronger X-rays (less dense areas) are convertet into lighter gray values. This is how the familiar X-ray images are created.
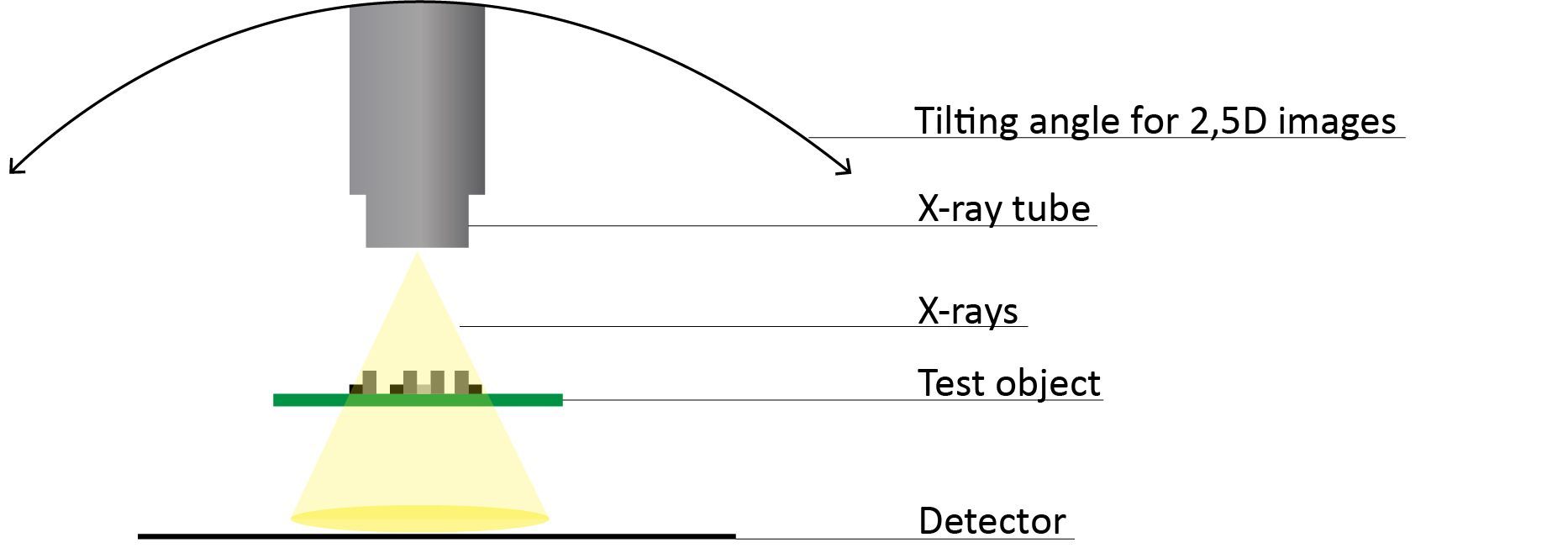
Schematic representation of an X-ray system with X-ray source, test object and detector
2D, 2,5D and 3D CT
There are three fundamental ways to take X-ray images: 2D, 2.5D and 3D CT.
2D
In 2D X-ray inspection, the X-rays are beamed frontally onto the test object. For double-sided PCBs and overlapping structures 2D X-ray inspection does not provide a clear result as the X-ray image cannot be evaluated clearly. But 2D inspection can lead to unclear results with single-sided PCBs as well: Open solder joints are not detected. As components become smaller and more complex, 2,5D inspection is establishing itself as the minimum requirement for X-ray systems in electronics manufacturing while the 2D inspection loses its importance.
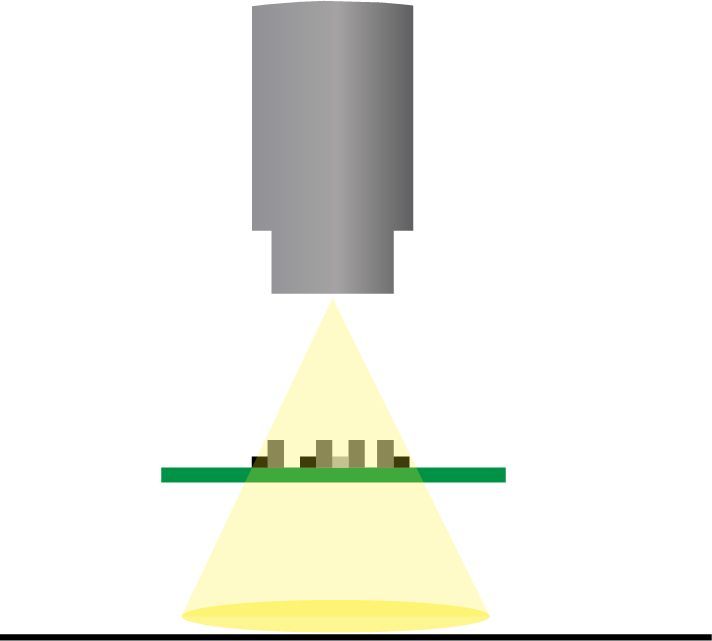
In 2D X-ray inspection, the X-rays strike the test object completely head-on.
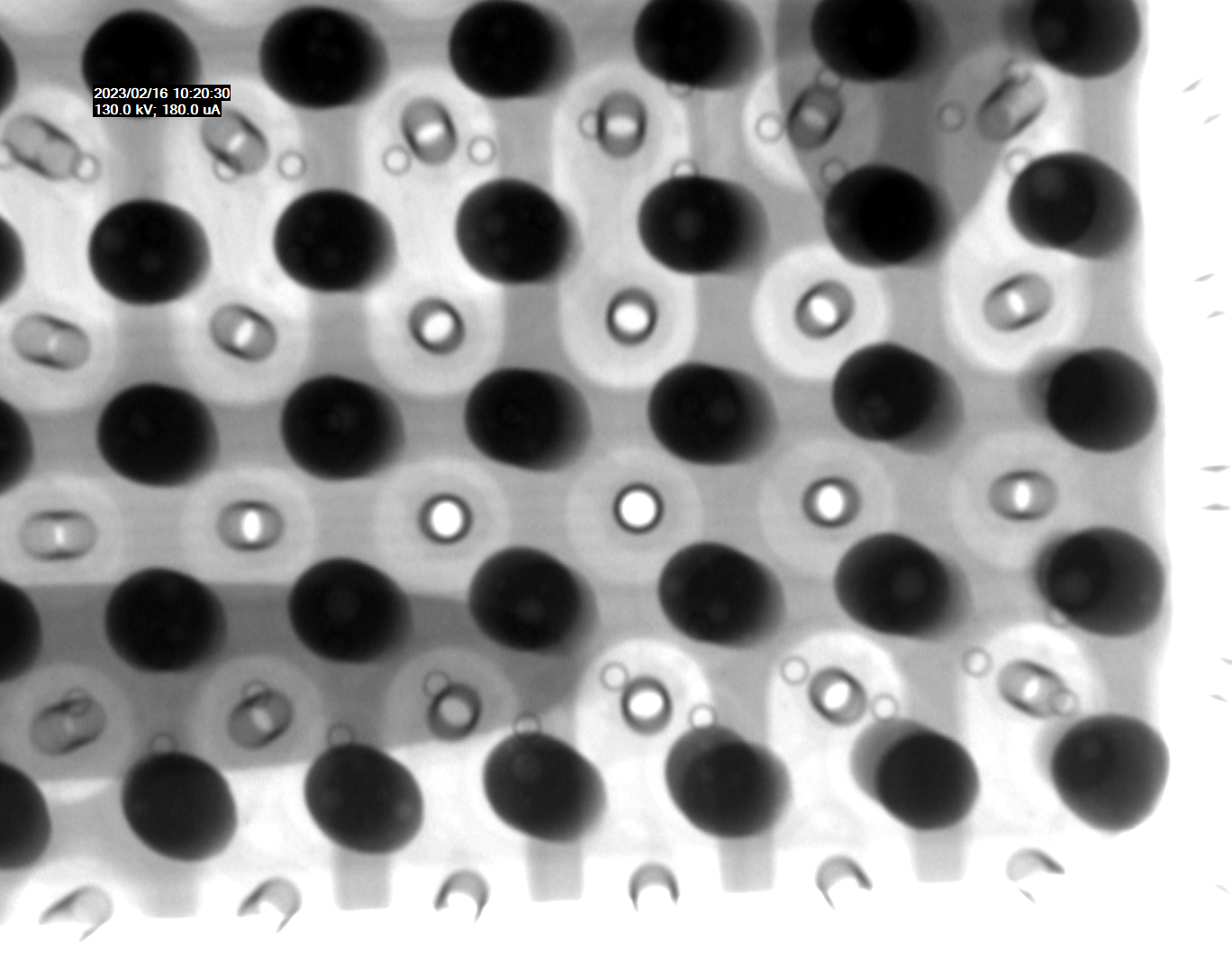
In the top view (2D view), almost all BGA balls therefore look perfectly round. Open solder joints are difficult or impossible to detect here.
2,5D
In 2.5D X-ray inspection, the X-ray radiation hits the region-of-interest from an adjustable angle, which enables an oblique view of components and solder joints. 2.5D inspection is particularly useful for inspecting components such as BGAs, as open solder joints can be detected. Solder penetration on THT components can also be measured with 2.5D X-ray inspection systems.
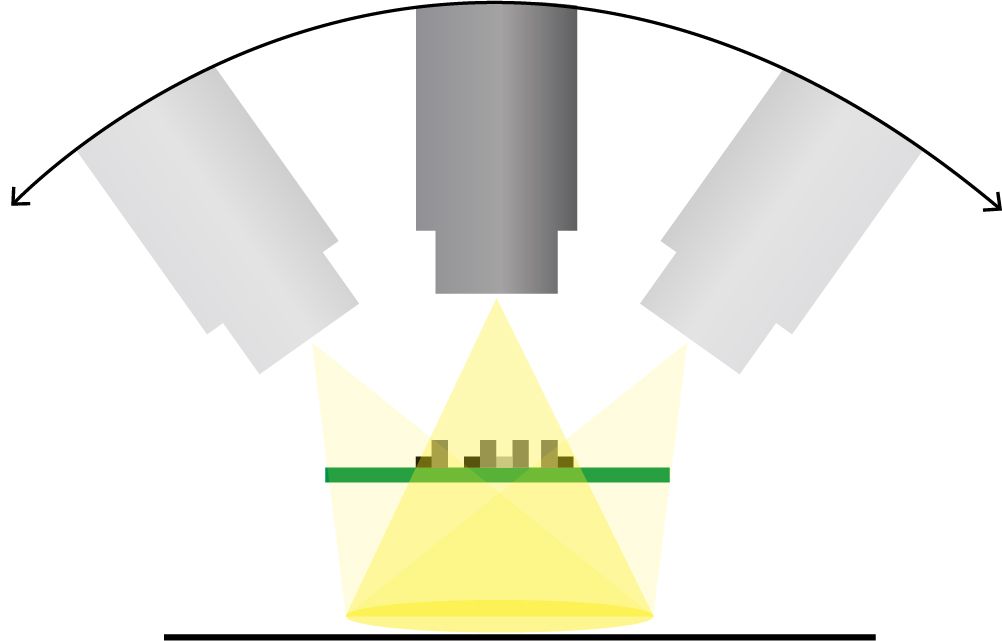
Due to the X-rays hitting the test object from different angles, the 2.5D X-ray image provides an oblique view of the ROI.
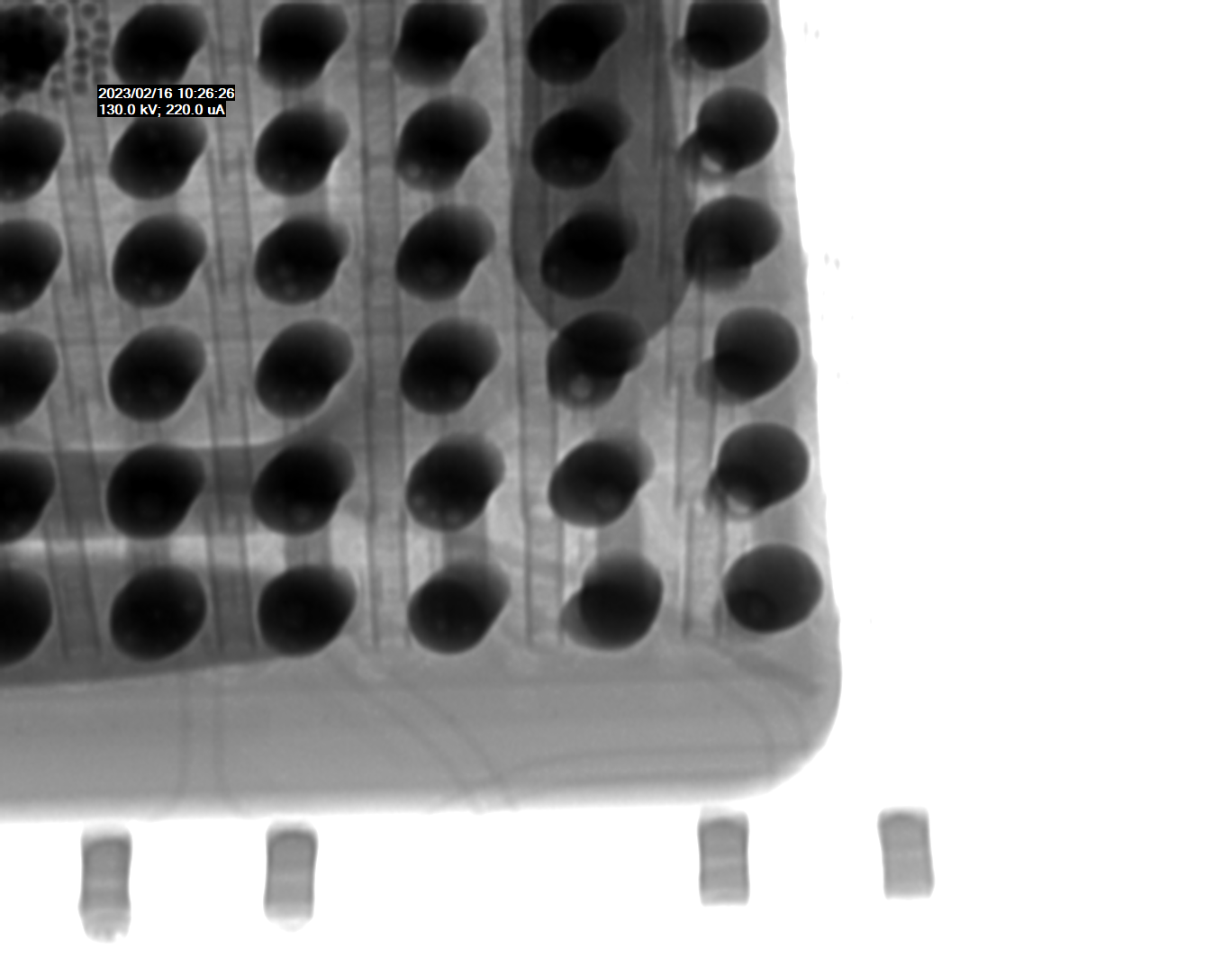
Only in the 2.5D view is it clear that there is no connection for most of the balls.
3D CT
The basis for 3D X-ray inspection is very similar to 2.5D image creation: The X-ray radiation hits the test object, which rotates at an angle of 360° around its own axis of rotation during image generation, from an adjustable angle. A specialized image processing program then generates a 3D reconstruction of the test object from the individual images taken during the recording process. This image reconstruction makes it possible to create and evaluate digital cross-section images of the assembly. For a high-quality CT image, it is recommended to take one image for each degree of rotation (360° rotation ≙ 360 frames). The total number of images thereby influences the cycle time of the system.
(left and top right) By rotating the test object and the detector, the test object is X-rayed from all sides. These images are the basis for a detailed 3D reconstruction (bottom right).
X-ray tubes – open vs. closed
X-ray tubes can generally be divided into two groups: Closed and open X-ray tubes. Both types of tubes do have their advantages and specific areas of application.
Closed X-ray tubes
A closed X-ray tubes is defined as such when it´s not possible to change the filament. Closed X-ray tubes are therefore always maintenance free. The closed housing maintains a certain vacuum level within the tube throughout it´s whole lifetime of 6000 to 10.000 X-ray hours on average. Most closed X-ray tubes can realize a resolution in the µm range.
Open X-ray tubes
An open X-ray tube is called "open tube" because it is possible to change the filament. Depening on the type, the filament must be changed every 300 to 1000 X-ray hours. Open X-ray tubes are thus not maintenance free. Since the tube can be opened, an external vacuum pump is needed for operation. Due to the vacuum created by the external pump the X-ray beam can be focused better, which allows detail detectability in the nanometer range to be achieved with open tubes.
Power and voltage at image generation
Power and voltage can be adjusted during X-ray inspection to allow a wide variety of materials to be X-rayed. The right range of power and voltage depends on the materials to be inspected: Materials with lowe density like aluminium need less voltage than materials with a high density like iron or gold. In general, X-ray images where more voltage has been applied will be brighter than images with less voltage because more radiation passes through the sample to the detector.
Detectors
For the generation of X-ray images, the Flat Panel Detector has established itself as the market standard has largely replaced the image intensifiers that were commonly used previously, because flat panel detectors produce high-contrast X-ray images even at low voltages. Nevertheless, suppliers of X-ray systems sometimes use their own technologies.
Radiation protection
In Germany, the Radiation Protection Ordinance applies to the operation of X-ray systems. According to this ordinance, all X-ray devices must meet the requirements for fully protective devices. This stipulates a complete lining of the system interior with lead, independent safety circuits for interrupting the current when doors are opened and a proven radiation emission of max. 3µ/Sv per hour at a distance of 0.1 meters from the touchable surface of the protective housing. This guideline value refers to X-ray radiation that is considered harmless to the operator. Before the system is installed at the place of use, it must be inspected by an independent expert and approved by the federal state-specific government authority.
All X-ray systems offered by SmartRep meet the requirements of RöV.
SmartRep cooperates in the field of industrial X-ray with Techvalley.