Robuste Steuergeräte ohne Fehlerschlupf produzieren
Dr. Julia Traut • 27. Juni 2022
SmartRep berät Graf-Syteco beim Aufbau einer neuen SMD-Linie
Mobile Baumaschinen, wie Straßenfräsen oder Schneeräumfahrzeuge, sind bei extremem Wetter im Einsatz; sie müssen zuverlässig und lange ihren Dienst tun. Dafür sorgt der Steuergerätehersteller Graf-Syteco aus Tuningen mit Koh Young Inspektionssystemen und einem sicheren Materialmanagementkonzept, das zusammen mit SmartRep beim Aufbau einer neuen SMD-Linie entwickelt wurde.
2020 startete Graf-Syteco trotz Corona ein Großprojekt: den Aufbau einer komplett neuen SMD-Linie inklusive Materiallager. „Genau das war die richtige Entscheidung“, sagt Geschäftsführer und Inhaber Jürgen E. Müller heute im Rückblick, denn jetzt könne man in der aktuellen Allokationssituation flexibel agieren. Als Generalunternehmer entwickelte, plante und koordinierte SmartRep das Projekt.
„Bei Graf-Syteco haben wir uns 2020 Gedanken darüber gemacht, dass wir unsere Produktionslinie effizienter, rückverfolgbar und automatisiert aufstellen wollen. Sicherheit im Materialfluss war ebenfalls ein Thema“, erinnert sich SMD-Leiter Darko Pejkovic.
Weil SmartRep zusammen mit Graf-Syteco ein tolles Konzept entwickelte und alles aus einer Hand liefern konnte, griff das schwäbische Unternehmen zu: „Wir sind nach wie vor gut betreut durch SmartRep. Egal welche Probleme auftauchen, es ist immer ein Mitarbeiter sofort da und hilft.“
Nikolai Knapp, Head of Sales bei SmartRep, begleitete Graf-Syteco bei diesem Großprojekt und analysierte den Bedarf: „Die Bedien- & Steuergeräte sind in mobilen Baumaschinen, wie Straßenfräsen, Bohranlagen für den Spezialtiefbau oder kommunale Nutzfahrzeuge verbaut. Dort kommt es auf Zuverlässigkeit und hohe Robustheit an. Daher war klar, dass Graf-Syteco beim Aufbau einer neuen Linie einen Schwerpunkt auf Qualitätsprüfung legt. Damit waren sie bei SmartRep an der richtigen Adresse: Unsere optischen Inspektionssysteme von Koh Young liefern genauste Messergebnisse in 3D – hier gibt es keinen Fehlerschlupf.“
Für Graf-Syteco sei die schnelle und einfache Programmerstellung der Inspektionssysteme sehr wichtig, weil oft mehrfach am Tag umgerüstet wird, um die hohe Produktvielfalt bei kleinen Losgrößen abzudecken. Benetzungswinkel, Anflusshöhe und natürlich auch die Bauteile – alles wird in 3D messtechnisch erfasst und in Echtzeit ausgewertet. Dadurch hat Graf-Syteco seine Produktionsqualität immer zu 100 Prozent im Blick. Neben den Inspektionssystemen von Koh Young setzte Graf-Syteco auf Bestücker und Drucker von Panasonic, Handlinglösungen von SmartRep und einen SMT-Ofen.
Mit dem Aufbau der neuen Linie sollte es möglich sein, 100% Traceability zu erreichen. „Damit dies gelingt, ist es unausweichlich bereits beim Wareneingang jedes Material zu überprüfen, mit einer Unique-ID zu versehen und die Bilder für spätere Rückverfolgbarkeit zu speichern. Wir haben also die Ist-Situation evaluiert und dann gemeinsam den neuen Weg mit einem intelligenten Wareneingang erarbeitet“, erzählt Nikolai Knapp.
„Wir waren eine Weile unterwegs und haben uns viele Systeme angeschaut. Das passendste Konzept haben wir bei SmartRep gefunden“, erinnert sich Darko Pejkovic. Alles SMD-Material wird nun bei Graf-Syteco über einen Wareneingangsscanner von MODI erfasst, mit einer Unique-ID versehen und dann in smarte Bauteilrollenregale einsortiert: „Nur über die Prüfung dieses Tisches läuft Material durch unsere Produktion“, sagt Pejkovic. Denn eine Vielzahl von verschiedenen Etiketten sind im Wareneingang eine Fehlerquelle, die eine Fehlbestückung nach sich ziehen kann.
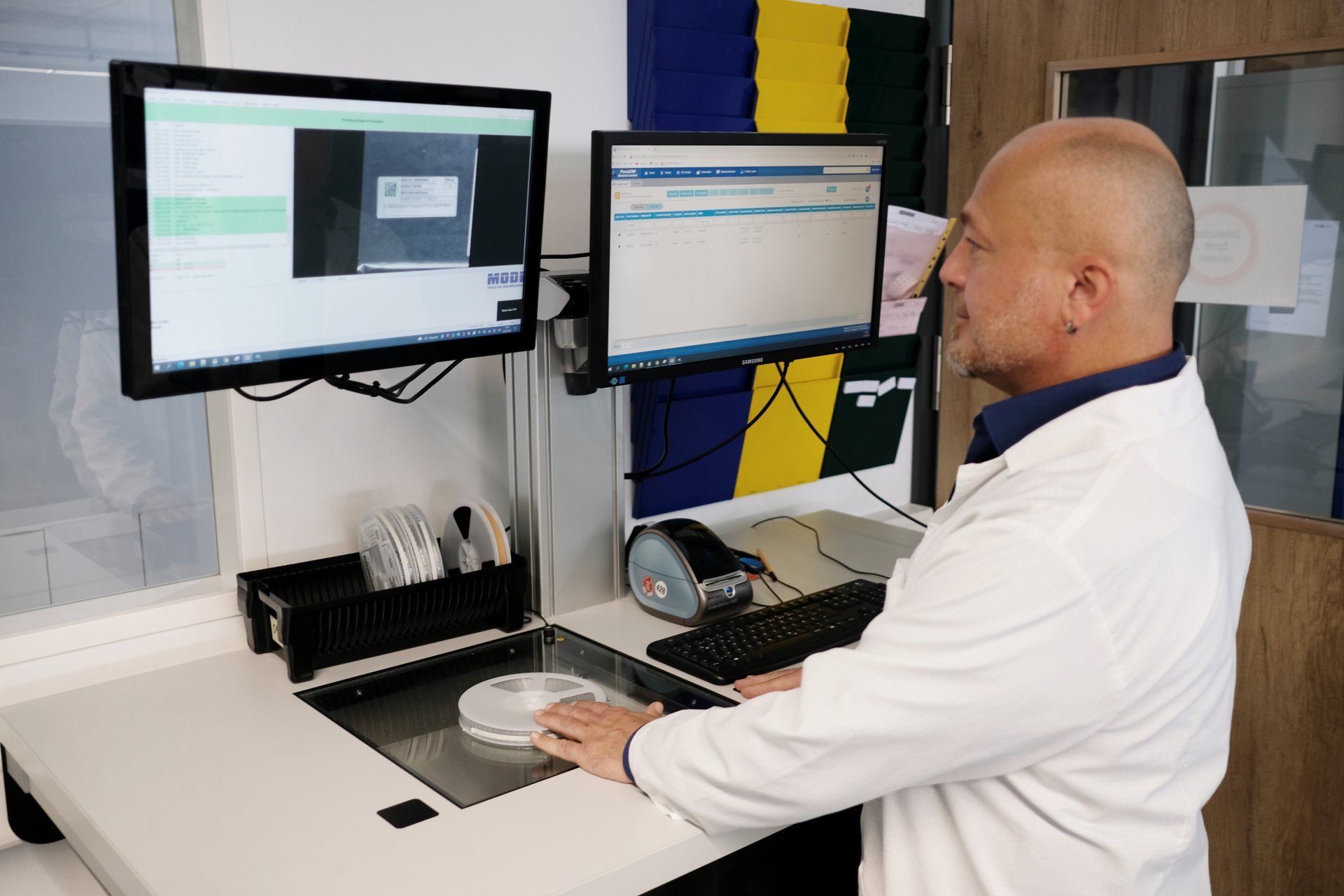
Alles SMD-Material wird nun bei Graf-Syteco über einen Wareneingangsscanner von MODI erfasst, mit einer Unique-ID versehen und dann in smarte Bauteilrollenregale einsortiert. (c) SmartRep
Dem hat Graf-Syteco nun mit der automatisierten Wareneingangslösung von MODI einen Riegel vorgeschoben. Damit werden Herstelleretiketten problemlos identifiziert, ausgelesen und die Bauteilrollen, vom System gestützt, fehlerfrei umgelabelt. Die Verwendung einer Unique-ID garantiert dabei 100% Traceability bereits ab dem Wareneingang. Dadurch, dass jede Rolle nach dem Etikettieren nochmals Gegengelesen wird und dann automatisch in die Materialmanagement Software gebucht wird, könne sich Graf-Syteco sicher sein, dass bereits mit der Vereinnahmung der Grundstein für die benötigte Qualität gelegt wurde, analysiert Nikolai Knapp.
Für den weiteren Warenfluss setzt Graf-Syteco auf Bauteilrollenregale von Inovaxe: „Sie haben uns durch den einfachen, funktionellen Aufbau überzeugt. Was soll da kaputt gehen? Ich habe keinen Roboter hinten dran, keinen Service, keine Wartung und keine Folgekosten durch irgendwelche Robotik oder Motoren“, sagt Pejkovic. Das intelligente Regal unterstützt den Bediener bei der Ein- und Auslagerung: Der Bediener scannt den Barcode der Rolle und lagert diese dann an einem beliebigen Platz ein. Intelligente Sensoren erkennen, an welchem Platz sich die Rolle befindet, und sie wird automatisch ins System eingebucht. Wird eine Rolle für einen Rüstauftrag benötigt, kann der Bediener im System nach der Unique-ID suchen oder direkt über die Marterialmanagement-Software des Bestückers anfordern. Die Systeme zeigen dem Bediener die Position der gesuchten Rolle an und ob genügend Material vorhanden ist. „Wir können damit sicher und gut produzieren“, so das Resümee des Fertigungsleiters.
Und auch Geschäftsführer Jürgen Müller ist von der Flexibilität der neuen Linie begeistert: „2021 wurde Elektronik knapp, und wir wurden von unseren Distributoren nicht so beliefert, wie wir dachten. Das konnten wir intern ganz gut spielen, weil wir eben – sobald wir Elektronik bekommen haben – dann die Leiterkarten auf der Maschine eingestellt haben. Insofern konnten wir im Jahresrückblick 2020/21 sehr gut performen.“
Video zum anwenderbericht:
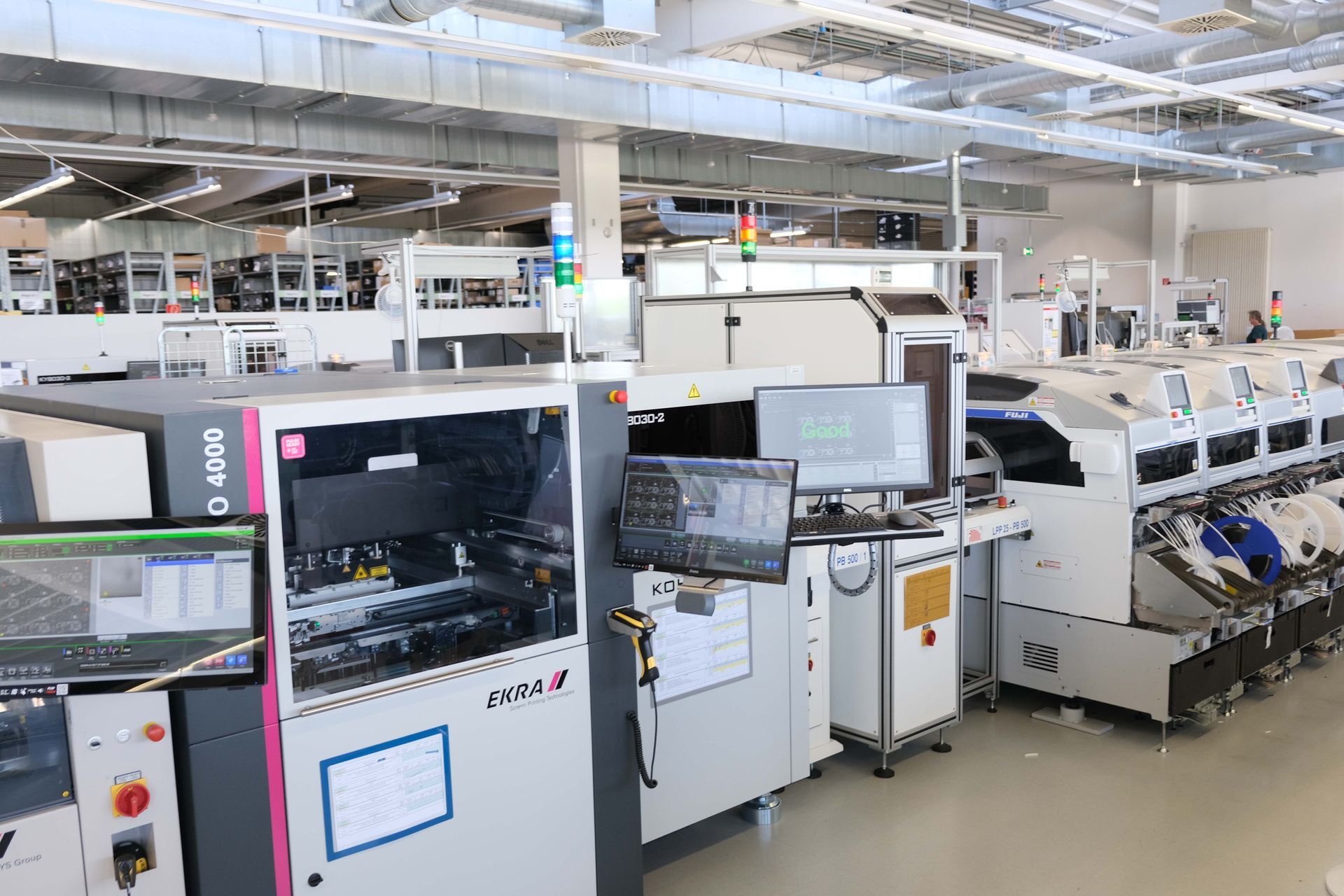

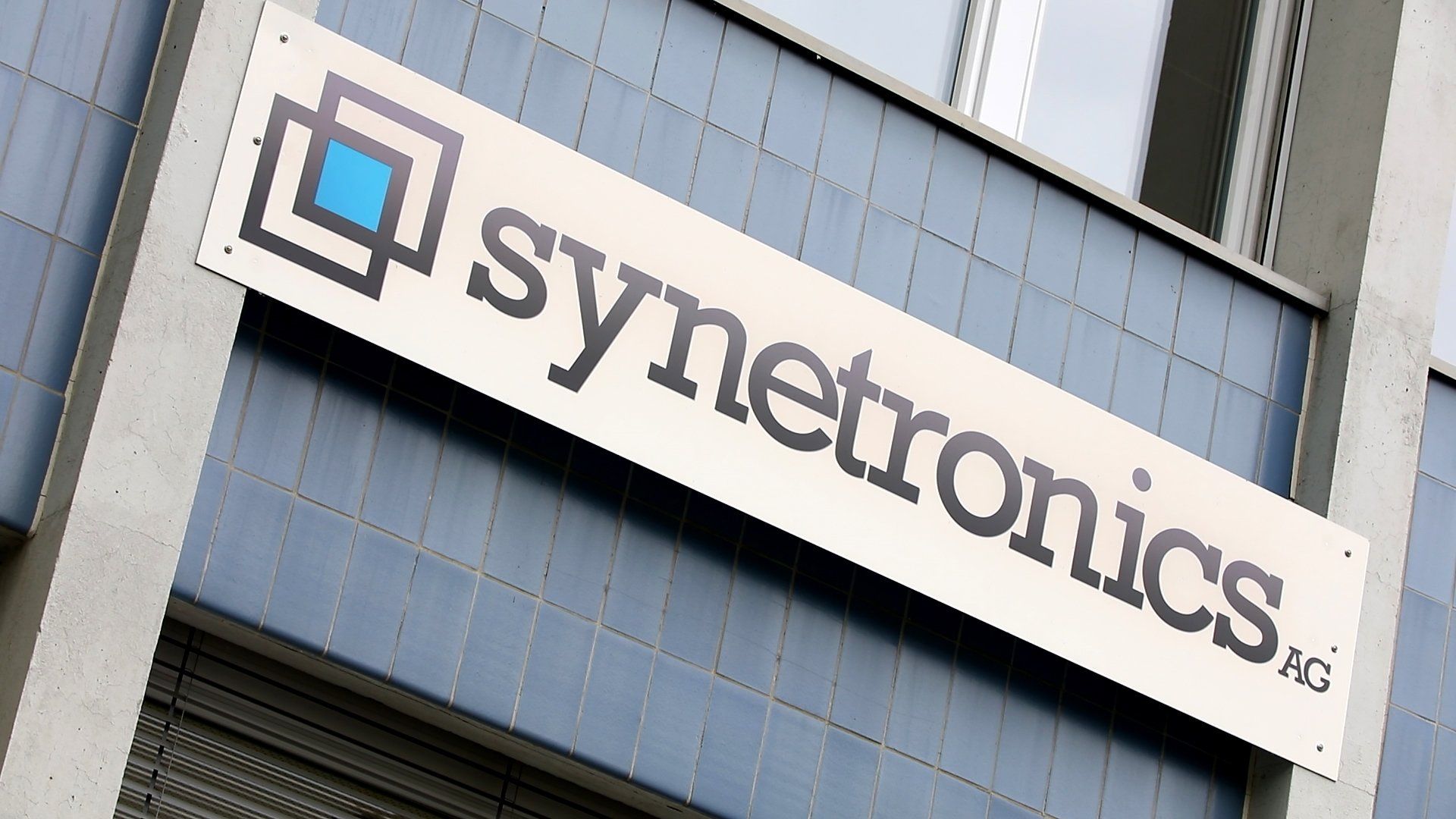
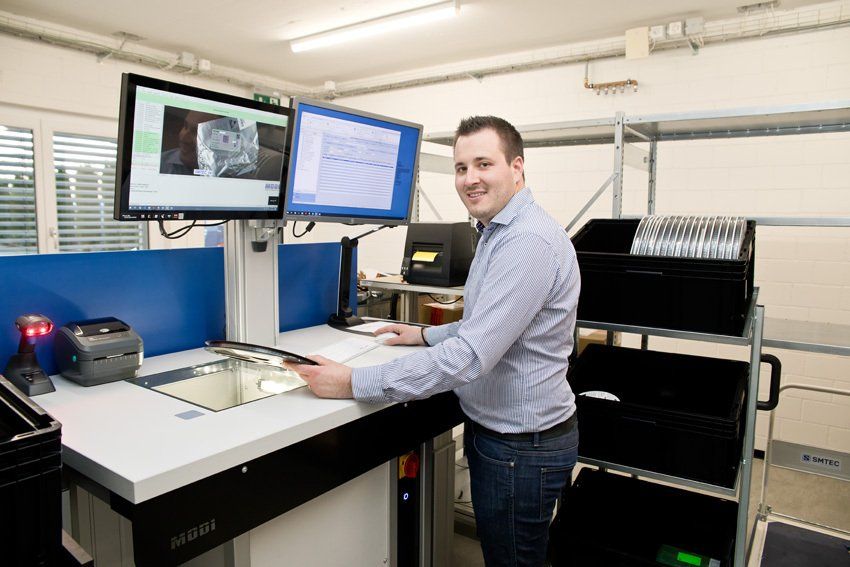
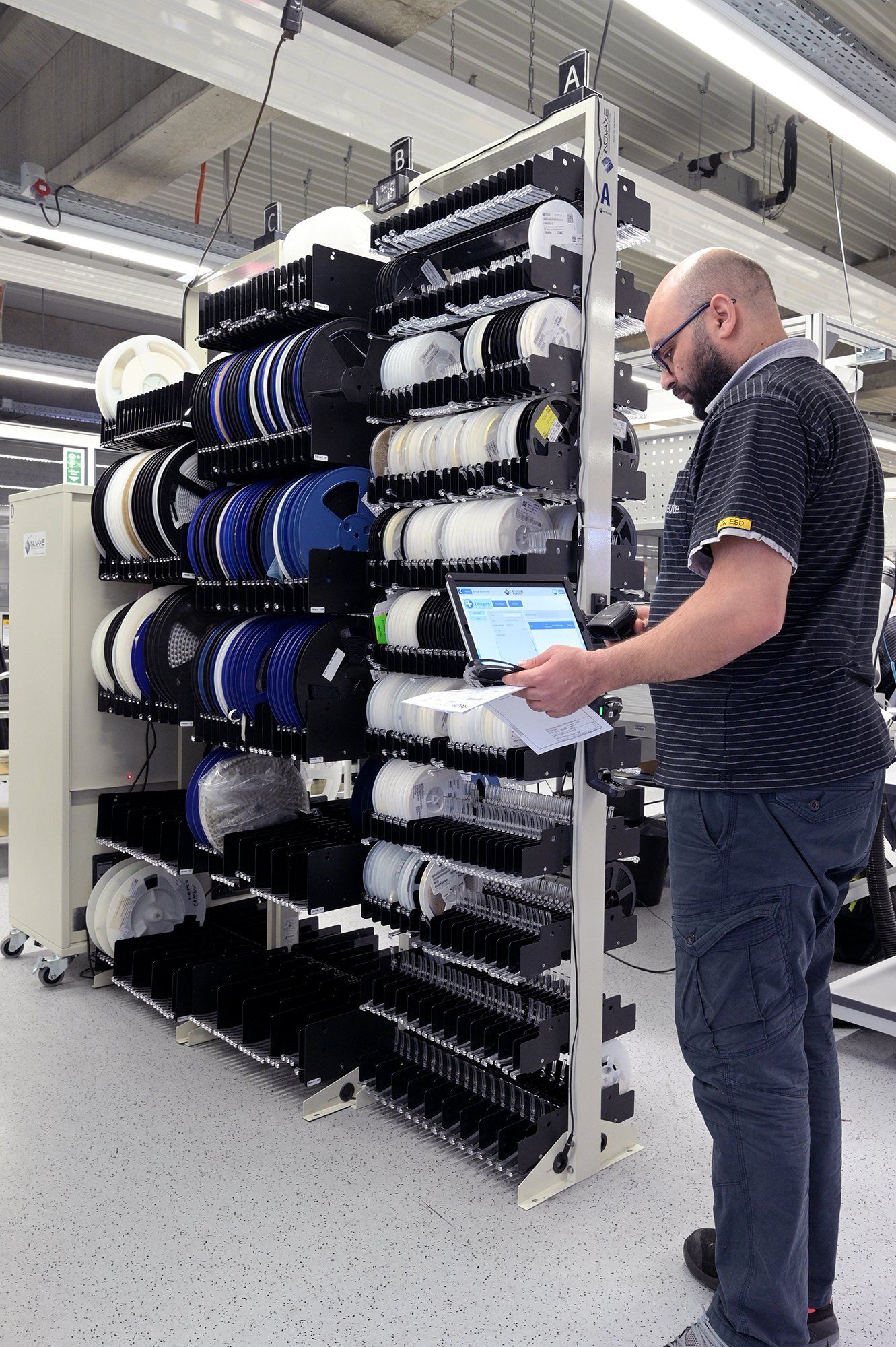
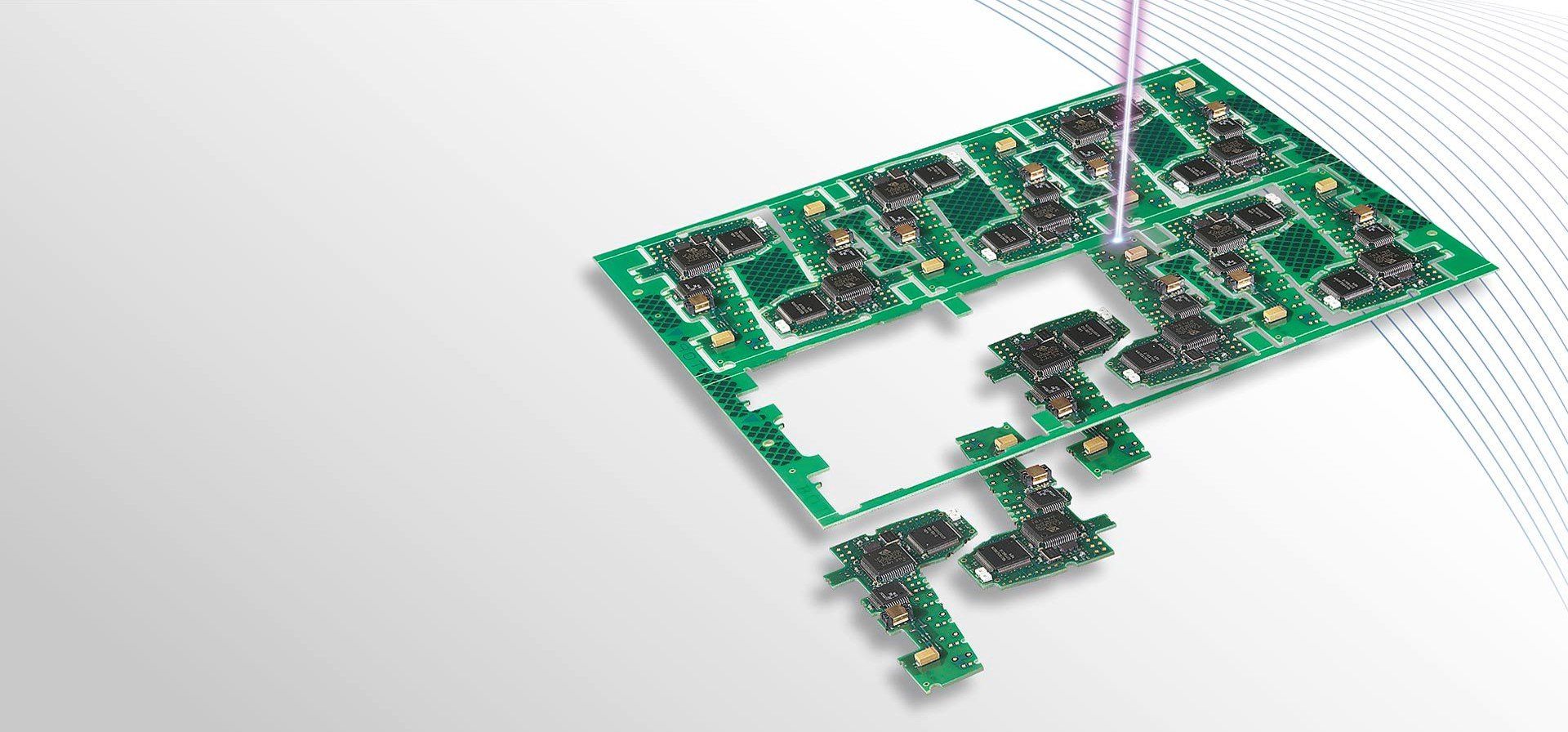